Schweißen entlang einer gewellten Naht
Zusammenfassung
In diesem Whitepaper wird anhand eines Beispielprozesses aus der Schweißtechnik der Nutzen von oddy zur Qualitätsüberwachung in der industriellen Massenstückfertigung aufgezeigt. In einem Prozess mit einer Ausstoßrate von etwa 3,4% wird dadurch eine fehlerbezogene Stückkostenreduktion von 0,340€ auf 0,104€ erreicht.
Zusätzlich zu dieser Stückkostenreduktion wird der Nutzen der werkstückbezogenen und kennzahlbasierten Qualitätssicherung bei der Anlagenüberwachung aufgezeigt. Durch detaillierten Prozesseinblick lassen sich Fehlerursachen besser finden und Prozessanpassungen quantitativ bewerten.
Prozessaufbau
Eine Schweißnaht entlang einer Kurve auf einer gewellten Oberfläche muss auf die Qualität der Schweißung mittels einer Sensordatenreihe untersucht werden.
Die Sensordaten unterliegen starken lokalen Schwankungen, die mit der Streuung auf der gewellten Oberfläche zusammenhängen. Daher eignet sich keine statische Schwellwertanalyse. Stattdessen sollen die Messwerte ortsaufgelöst berechnet und dann mit verschiedenen Messreihen, welche unter denselben Bedingungen entstanden sind, verglichen werden.
So werden Fehler identifiziert, die über die statistisch erwartete Mess- und Prozessschwankung hinausgehen.
Konfiguration
Zur korrekten Auswertung der Prozessdaten muss zunächst die Prozesskonfiguration möglichst präzise erfasst werden. Das stellt sicher, dass nur Prozesse miteinander verglichen werden, welche auch unter identischen Bedingungen durchgeführt wurden.
Die Prozesskonfiguration ist zweigeteilt. Auf der einen Seite stehen die Konfigurationsparameter, mit der die Laseroptik geometrisch für die Werkstücke eingerichtet wird. Auf der anderen Seite stehen die Kalibrierungsparameter, welche in regelmäßigen Wartungsintervallen an der Optik vermessen werden. Beide Kategorien von Daten werden für eine zuverlässige Kennzahlbestimmung benötigt.
Die Darstellung zeigt den geometrischen Verlauf der Schweißnaht auf der Werkstückoberfläche mit dem Intensitätsprofil des Laserpunktes.
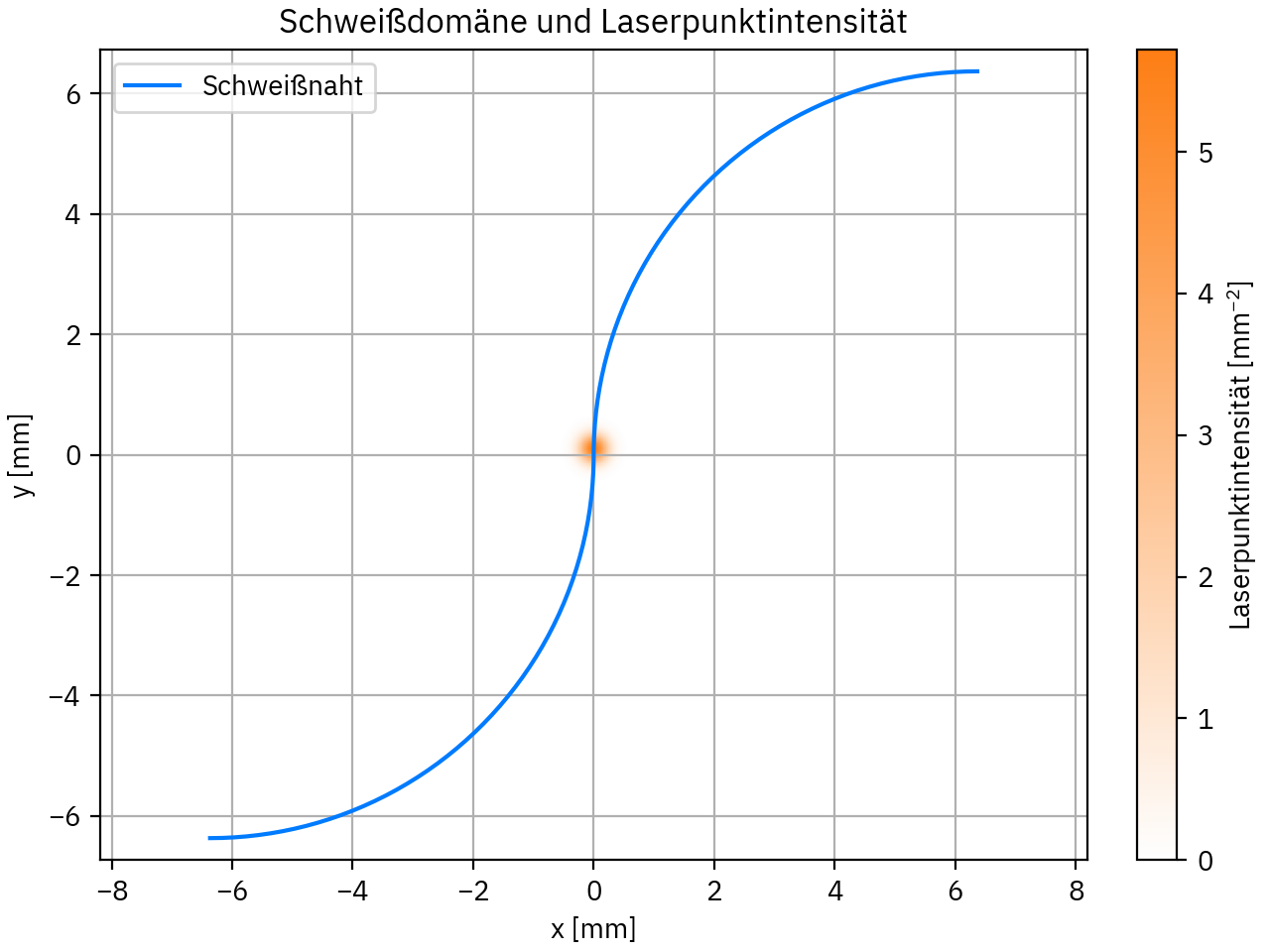
Maschinenkonfiguration
Die Maschinenkonfiguration enthält folgende Informationen:
-
Prozesszeit [ms]
Die Prozesszeit ist das Zeitintervall, innerhalb dessen die Laseroptik die vorgegebene Geometrie abfährt.
-
Geschwindigkeit [mm/ms]
Die Geschwindigkeit ist die Oberflächengeschwindigkeit des Laserpunktes auf dem bearbeiteten Werkstück.
Die folgende Darstellung zeigt den geometrischen Verlauf des Pfades auf dem Werkstück. Zur Veranschaulichung der Geschwindigkeit ist zu jeder vollen Millisekunde ein Punkt auf dem Pfad markiert. Die Laseroptik fährt den Pfad von unten links nach oben rechts ab.
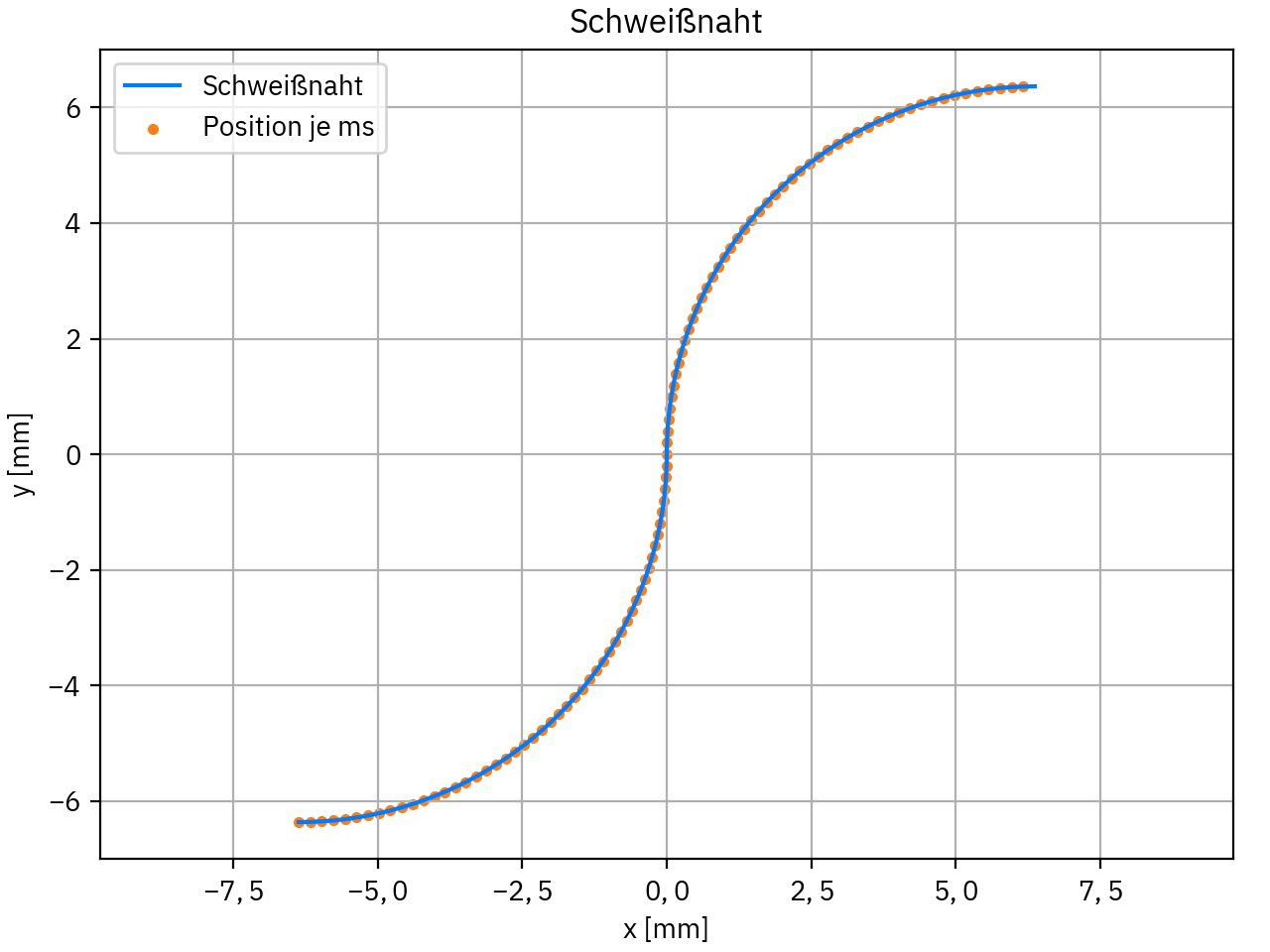
Maschinenkalibrierung
Die Maschinenkalibrierung erfolgt in regelmäßigen Abständen. Dabei wird die Ausdehnung des Laserpunktes in der Fokalebene vermessen und als Wartungsparameter hinterlegt. Dabei wird ebenso die Messfrequenz der Apparatur eingestellt.
-
Fokalpunktbreite [mm]
Die Breite des Laserpunktes in der Fokalebene. Der Laserpunkt wird dabei als kreisförmig normalverteilt angenommen. Die vermessene Breite entspricht drei Standardabweichungen und enthält 98,9% der integrierten Intensität.
-
Messfrequenz [kHz]
Die Messfrequenz gibt die Zahl der Sensormessungen pro Zeit an.
Die Darstellung zeigt die modellierte Form des Laserpunktes in der Fokalebene gemeinsam mit der gemessenen Breite.
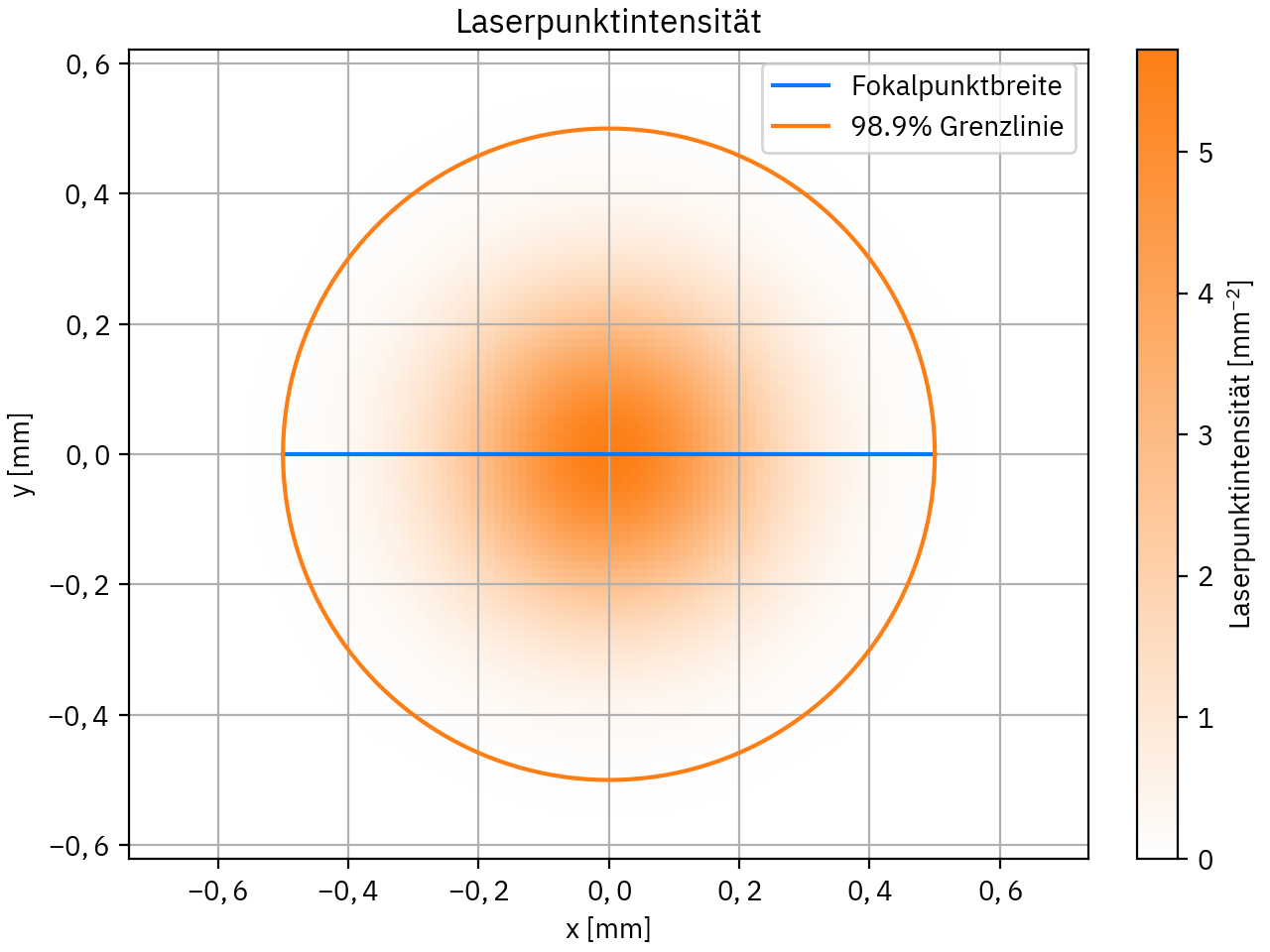
Messung
Die Prozesssensorik nimmt einen Wert pro Messung für die gesamte Prozessdauer mit der eingestellten Messfrequenz. Aufgrund der rauen Oberfläche streuen die Werte um das mittlere Profil. Die Rohmessung ist ein temperaturäquivalenter Strahlungswert um einen fest eingestellten Basiswert.
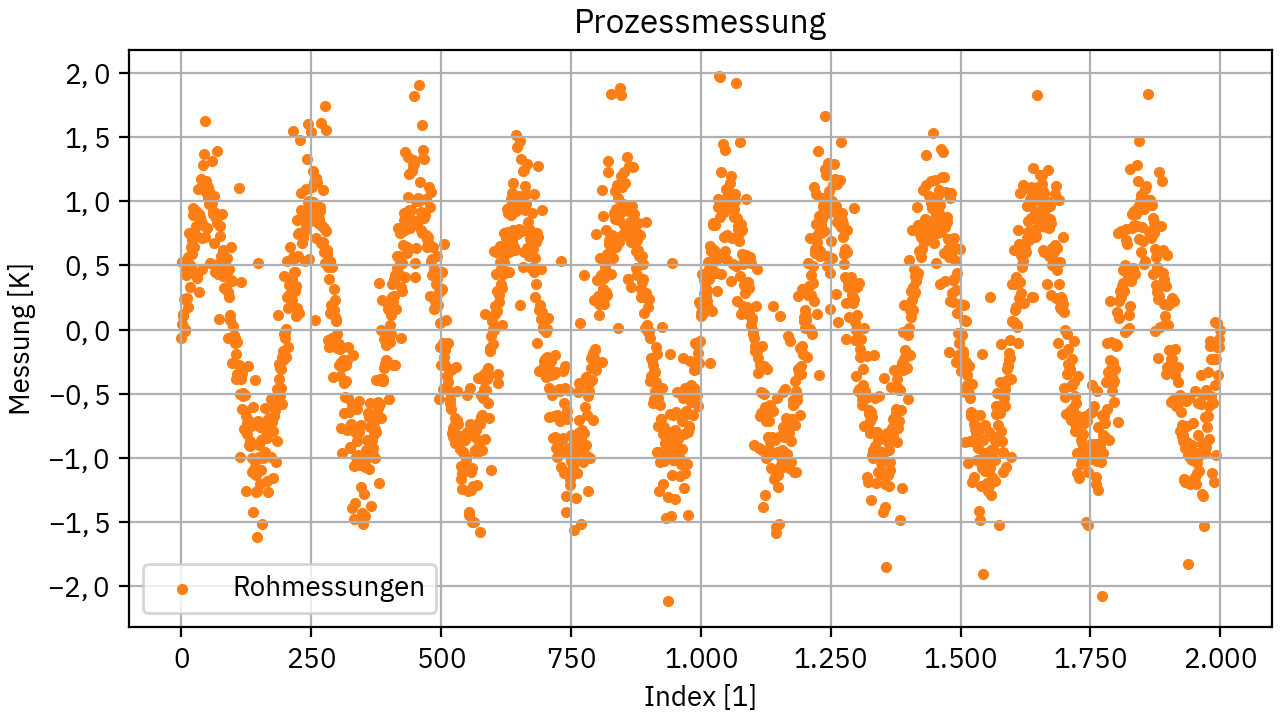
Auswertung
Die Einzelmessungen einer Messreihe streuen aufgrund technischer Eigenschaften und kleiner Schwankungen in Werkstück und Apparatur um einen lokalen Mittelwert. Da sich zudem die vom Laser aufgebrachte Strahlungsintensität auf der Oberfläche diffusiv verteilt, ist es vernünftig, die Messwertstreuung ebenso lokal auszumitteln. Zu diesem Zweck werden die Messdaten lokal mit einer Gewichtung ausgemittelt, deren Form und Ausdehnung näherungsweise derjenigen des Laserfokalpunktes entspricht.
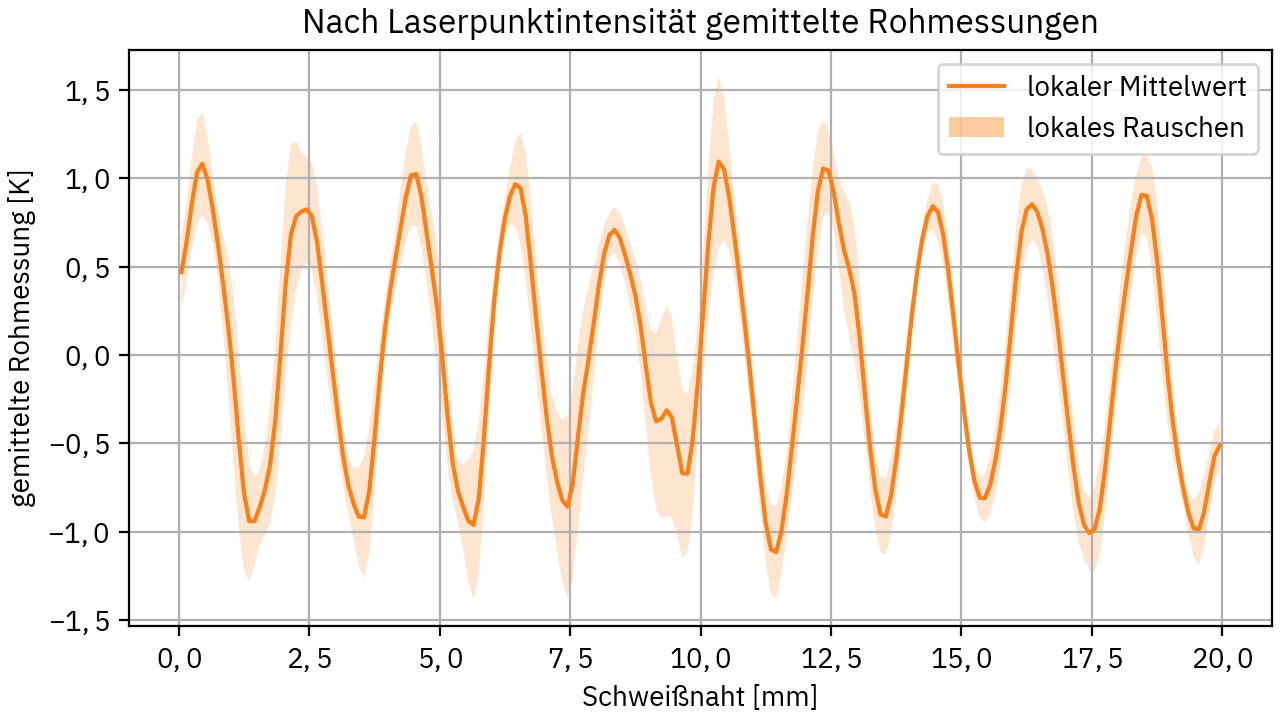
Diese gemittelte Datenreihe kann nicht sinnvoll mit konstanten Schwellwerten überwacht werden, da sie ein stark schwankendes Mittelwertprofil abbildet. Um zuverlässig Fehlproduktionen zu finden, die stark außerhalb der Norm liegen, kann man die Daten des einzelnen Prozesses mit der ortsaufgelösten statistischen Verteilung von vielen anderen Messungen vergleichen.
Bauteilbewertung
Technische Bewertung
Mithilfe der Messreihenvergleichsmethode lassen sich zusammenhängende Bereiche identifizieren, auf denen die Messwerte signifikant außerhalb der erwarteten statistischen Grenzen liegen. Zu diesem Zweck betrachtet man etwa die ortsaufgelöste Anomaliestärke. Sie berechnet sich aus der lokalen Mittelwertabweichung geteilt durch die statistische Standardabweichung.
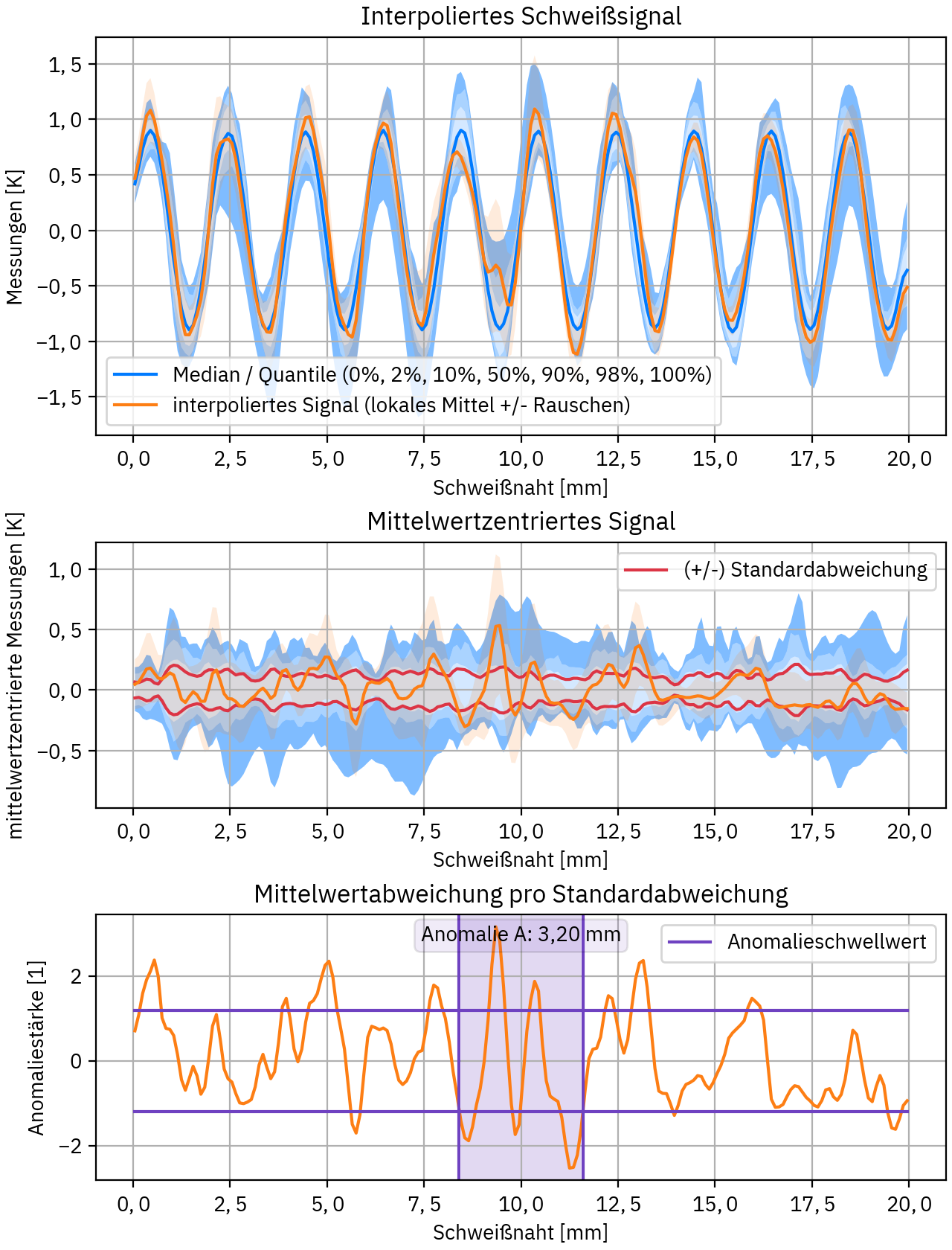
Für diese abgeleitete Kennzahl kann man nun durch die Prozessphysik und die Erfahrung mit der Fertigung Größen- und Stärkenschwellwerte festlegen, welche möglichst präzise diejenigen Prozessanomalien erkennen, welche in der Qualitätsprüfung als nicht OK markiert werden sollen.
Die vorige Abbildung zeigt ein Beispiel für einen solchen Prozess, bei dem etwa eine Oberflächenverformung oder Verunreinigung zu einem stark abweichenden Messprofil führt.
Wirtschaftliche Analyse
Um die Zuverlässigkeit der Methodik und der Schwellwerte, sowie den wirtschaftlichen Nutzen der Qualitätskennzahlen einzuschätzen, kann man die Trennschärfe der Methodik für eine Bauteilstichprobe bestimmen, deren Qualitätsmerkmale auf anderem Wege bekannt sind.
-
Defekt ausgeliefert - falsch OK
Das Bauteil ist nicht OK, aber der Fehler wird nicht bemerkt. Das Bauteil wird trotzdem ausgeliefert und verursacht Folgekosten durch Reparatur, Ersatz oder Reputationsverlust.
-
Fehlerfrei entsorgt - falsch nicht OK
Das Bauteil ist OK, wird aber fälschlicherweise anders eingeschätzt. Das Bauteil wird entsorgt und abgeschrieben, obwohl es hätte verkauft werden können.
Typischerweise sind defekt ausgelieferte Bewertungen wesentlich teurer als fehlerfrei entsorgte. Dementsprechend können die Schwellwerte genau nach betriebswirtschaftlichen Einschätzungen eingestellt werden.
Die folgende Abbildung zeigt eine beispielhafte Verteilung für eine Stichprobe von 1.000 Bauteilen.
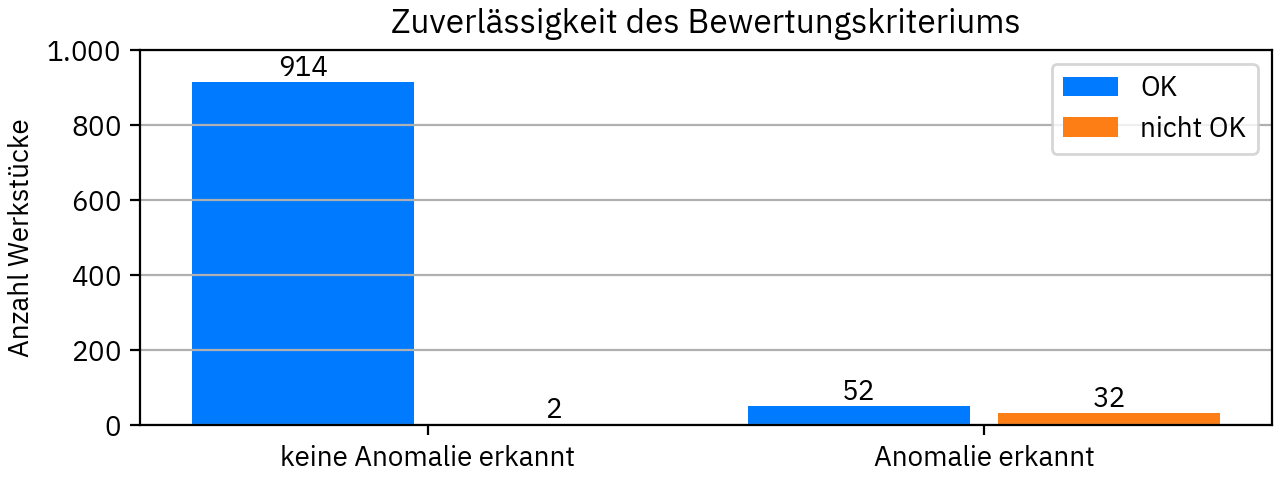
Dafür ergibt sich folgende Bewertungsgüte.
Bauteile | Bewertung | Merkmal | Anzahl | Anteil |
---|---|---|---|---|
gesamt | 1.000 | 100,0% | ||
keine Anomalie erkannt | 916 | 91,6% | ||
OK | 914 | 91,4% | ||
nicht OK | 2 | 0,2% | ||
Anomalie erkannt | 84 | 8,4% | ||
OK | 52 | 5,2% | ||
nicht OK | 32 | 3,2% |
Nimmt man nun an, dass ein defekt ausgeliefertes Bauteil Folgekosten von 10€ und ein entsorgtes Bauteil Abschreibungen von 1€ verursacht, ergibt sich damit die folgende Fehlerkostenschätzung:
QS-System | Fehlerquelle | Quote | Kosten / Fehler | Kosten / Teil |
---|---|---|---|---|
ohne oddy | 3,4% | 0,340€ | ||
defekt ausgeliefert | 3,4% | 10€ | 0,340€ | |
defekt entsorgt | 0,0% | 1€ | 0,000€ | |
fehlerfrei entsorgt | 0,0% | 1€ | 0,000€ | |
mit oddy | 8,6% | 0,104€ | ||
defekt ausgeliefert | 0,2% | 10€ | 0,020€ | |
defekt entsorgt | 3,2% | 1€ | 0,032€ | |
fehlerfrei entsorgt | 5,2% | 1€ | 0,052€ |
In diesem Szenario ergibt der Einsatz von oddy im Vergleich zu einem QS-System, welches die detaillierten Fehlerbilder nicht erkennt eine erwartete Kostenreduktion um 69,4% durch verbesserte Qualitätskontrolle von 0,340€ auf 0,104€ pro Bauteil.
Anlagen- und Chargenüberwachung
Zusätzlich zur niedrigeren Ausfallquote in ausgelieferten Bauteilen stellt das oddy-System einen präzisen Einblick in die Prozessdaten zur Verfügung. Damit ist es möglich, laufend Prozessveränderungen zu analysieren und zu bewerten. So steht ein weiteres Werkzeug zur Verfügung, um Fehlerursachen schnell zu finden und große Qualitätsprobleme frühzeitig zu vermeiden.
Indem die Prozessdaten immer mit einem Satz Prozessdaten verglichen werden, der regelmäßig erneuert wird, lassen sich Trends in den Prozessdaten abbilden und aus deren Verteilungsbreite auch die Prozessstabilität überwachen. Dies kann frühzeitig auf Wartungsbedarf, Chargenprobleme oder Probleme in Vorprozessen hindeuten.
Die folgende Abbildung zeigt die Prozessdatenverteilung von mehreren hundert Messungen und deren Mittelwertdrift durch zeitliche Einteilung in 4 gleichgroße Untermengen.
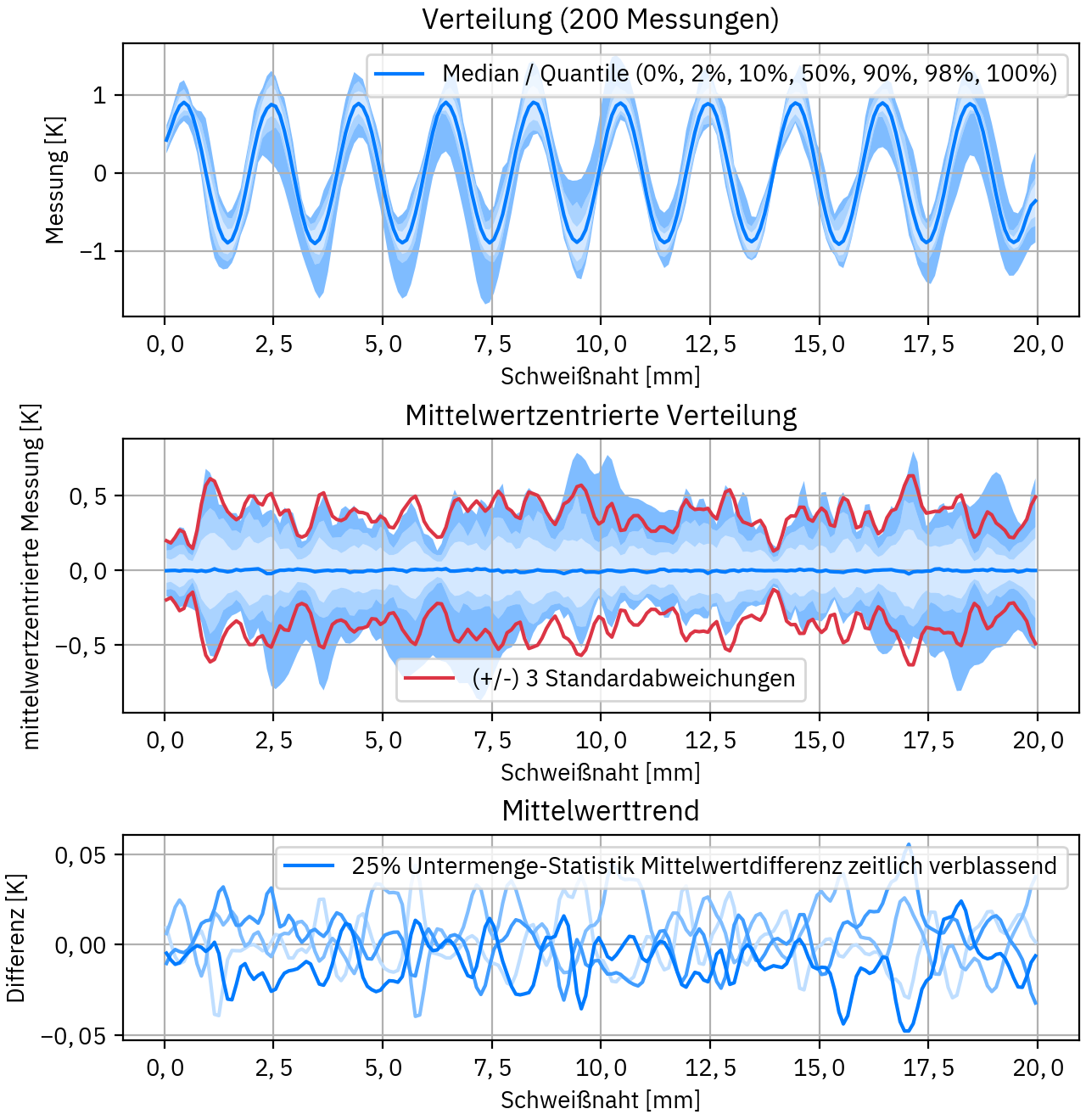
Fazit
Durch ortsaufgelöste Prozessdatenanalyse kann oddy Fehlerbilder identifizieren, welche nicht durch Analysen mit konstanten Schwellwerten gefunden werden können. Durch diesen Vorteil ist es möglich, die Fehlerfolgekosten von defekt ausgelieferten Bauteilen drastisch zu reduzieren. Zusätzlich liefern detaillierte Prozesseinblicke die Möglichkeit, frühzeitig bei Betrieb mit erhöhten Fehlerraten zu analysieren und zu intervenieren.
Die für diese Fallstudie verwendeten Prozessdaten sind zu Demonstrationszwecken streng zufällig erzeugt worden.