Laserhärten auf einer rechteckigen Oberfläche
Zusammenfassung
In dieser Fallstudie wird die Messreihe einer Laseroptik ausgewertet, mit deren Hilfe eine Metalloberfläche durch Bestrahlung schnell erhitzt und dadurch ausgehärtet wird. oddy ist dabei in der Lage fortlaufend Qualitätsschwankungen zu erkennen und Fehlproduktionen zuverlässig auszusortieren. Bei einer angenommenen Grundfehlerrate von 4,1% der prozessierten Bauteile senkt die oddy-basierte Qualitätssicherungsstrategie die fehlerbezogenen Stückkosten von 0,410€ auf 0,104€ um 74,6%.
Zusätzlich zu der Stückkostenreduktion erlaubt die kennzahlbasierte und werkstückbezogene Qualitätskontrolle eine sichere Identifikation von Prozess- oder Chargenproblemen, da detaillierte Grafiken und Statistiken zum Verständnis des Prozesses zur Verfügung stehen.
Prozessaufbau
Eine Metalloberfläche wird durch Laserbestrahlung kurz hocherhitzt, um sie auszuhärten. Dieser Vorgang soll flächendeckend auf Mängel untersucht werden, die etwa durch Verformung oder Verunreinigung der Oberfläche verursacht sein können. Dazu wird während des Bestrahlens der Oberfläche die Position und die Leistungsaufnahme sowie die Oberflächentemperatur des Werkstücks aufgezeichnet.
Aus den Messreihen kann mithilfe der geometrischen Information über das Bauteil eine Karte der aufgebrachten Energiedichte und der erreichten Oberflächentemperatur rekonstruiert werden. Damit lassen sich etwa Flecken aus entflammbaren oder kühlenden Rückständen gut identifizieren.
Konfiguration
Die auszuhärtende Oberfläche ist immer rechteckig und wird von einer Laseroptik in vertikalen, parallelen Strichen von unten nach oben (y-Koordinate steigend) und von links nach rechts (x-Koordinate steigend) abgefahren. Dabei vermisst die Optik den Zählindex des parallelen Striches, sowie die Oberflächentemperatur, die aktuelle Leistungsaufnahme und die vertikale Position.
In horizontaler Richtung wird das Bauteil mit gleichbleibender Geschwindigkeit abgefahren. Die folgende Abbildung zeigt die Ausdehnung des Laserfokalpunktes in Relation zur auszuhärtenden Oberfläche.
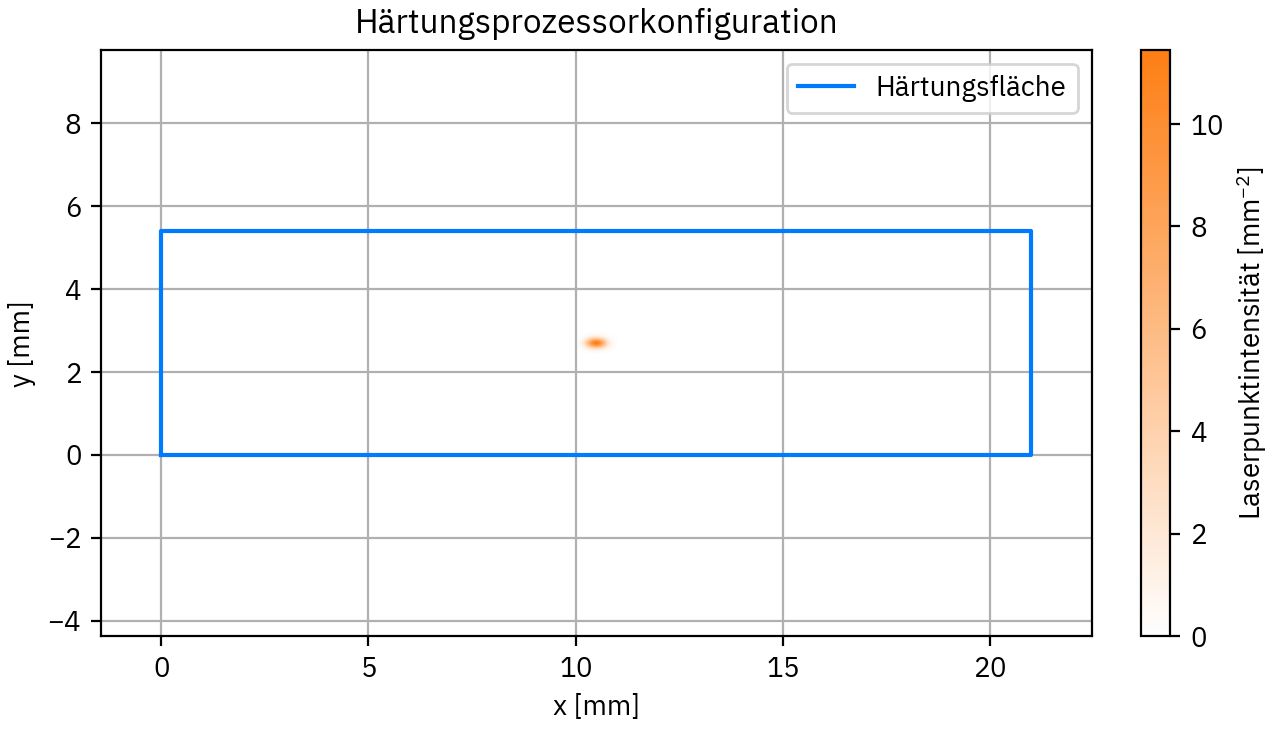
Maschinenkonfiguration
Die Maschinenkonfiguration enthält folgende Informationen:
-
horizontale Geschwindigkeit [mm/ms]
Die horizontale Geschwindigkeit ist die gleichbleibende Geschwindigkeit des Laserpunktes in horizontaler Richtung (x-Koordinate) auf dem bearbeiteten Werkstück.
-
Flächenausdehnung [mm|mm]
Die Ausdehnung gibt die Größe der bearbeiteten Fläche in Kantenlängen entlang x- und y-Koordinate an. Beide Werte werden in Millimeter vermessen.
Die folgende Darstellung zeigt den Zeitverlauf des Lasers im ansteigenden Farbverlauf. Der Laserpunkt setzt links unten an und fährt in vertikalen Strichen über die Werkstückoberfläche.
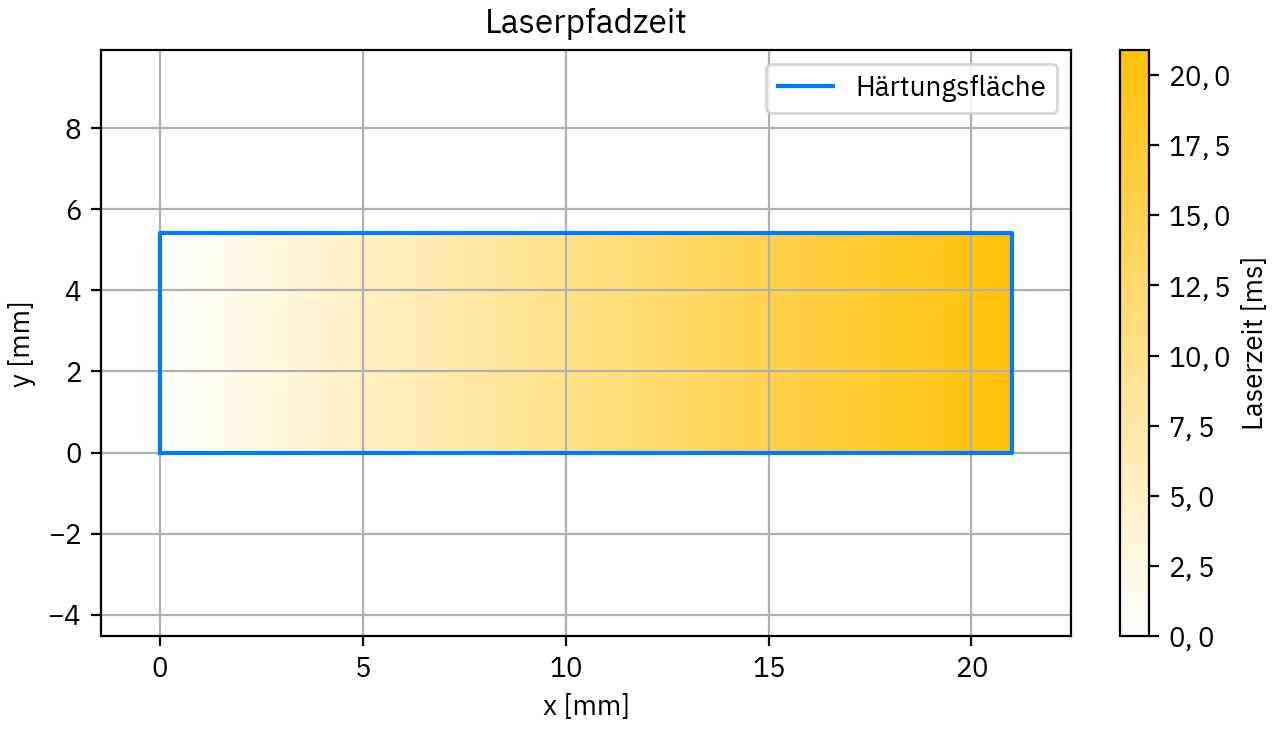
Maschinenkalibrierung
Die Maschinenkalibrierung erfolgt in regelmäßigen Abständen. Dabei wird die Ausdehnung des Laserpunktes in der Fokalebene vermessen und als Wartungsparameter hinterlegt. Dabei wird ebenso die Messfrequenz der Apparatur eingestellt.
-
Fokalpunktbreite [mm|mm]
Die Breite des Laserpunktes in der Fokalebene. Der Laserpunkt wird dabei als ellipsoid normalverteilt angenommen. Das vermessene Kreuz entspricht je drei Standardabweichungen in jede Richtung und enthält 98,9% der integrierten Strahlungsintensität.
-
Messfrequenz [kHz]
Die Messfrequenz gibt die Zahl der Sensormessungen pro Zeit an.
Die Darstellung zeigt die modellierte Form des Laserpunktes in der Fokalebene gemeinsam mit der gemessenen Breite.
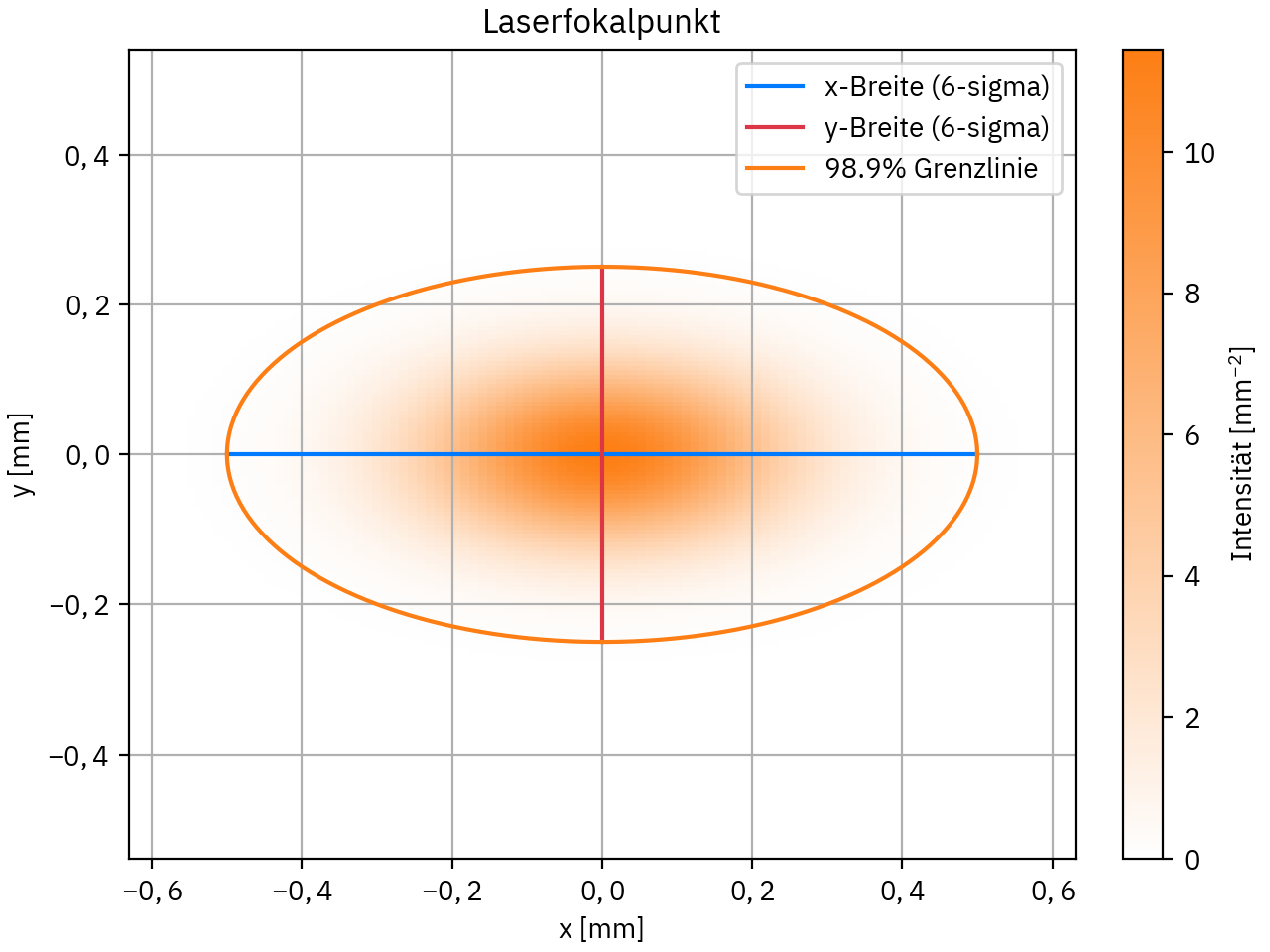
Messung
Der Prozesssensor sammelt während der Oberflächenhärtung folgende Daten:
-
Index [1]
Der Zähler für den vertikalen Scanvorgang.
-
y-Position [mm]
Die vertikale Position des Laserfokalpunktes auf der Oberfläche.
-
Temperatur [K]
Die gemessene Oberflächentemperatur.
-
Leistung [W]
Die Leistung der Laserlichtquelle.
Die folgende Darstellung zeigt die aufgezeichneten Rohdaten für einen Beispielprozess.
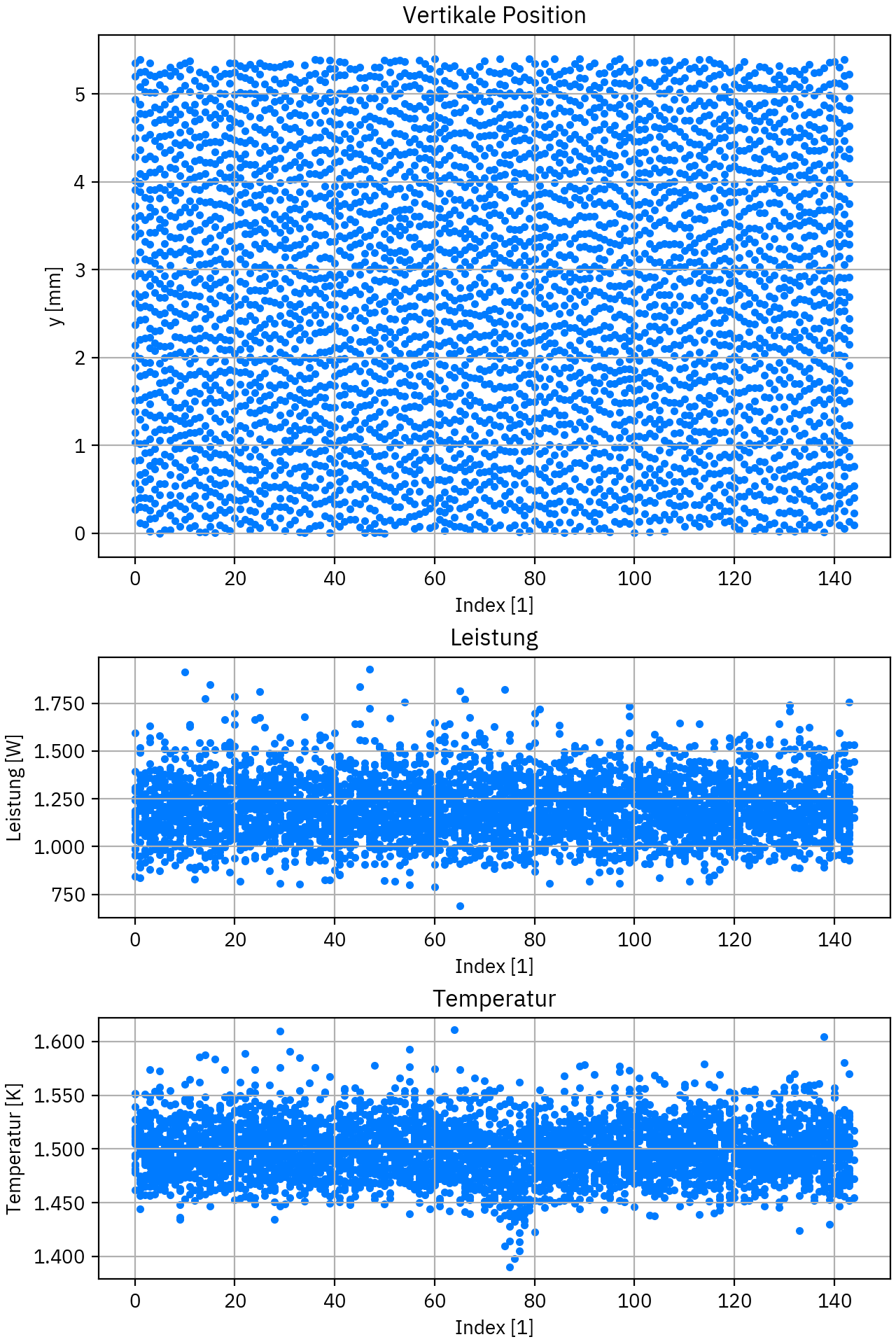
Auswertung
Die Einzelmessungen einer Messreihe streuen aufgrund technischer Eigenschaften und kleiner Schwankungen in Werkstück und Apparatur um einen lokalen Mittelwert. Um die diffusive Verteilung der aufgebrachten Strahlungsenergie und gemessenen Temperatur zu berücksichtigen, kann man die vermessenen Daten lokal mitteln. Die Mittelung folgt dabei in ihrer Gewichtung der Intensität des Laserfokalpunktes auf der Oberfläche.
Die Temperatur kann dabei direkt aus der Lage der Messpunkte und der Messwerte interpoliert werden.
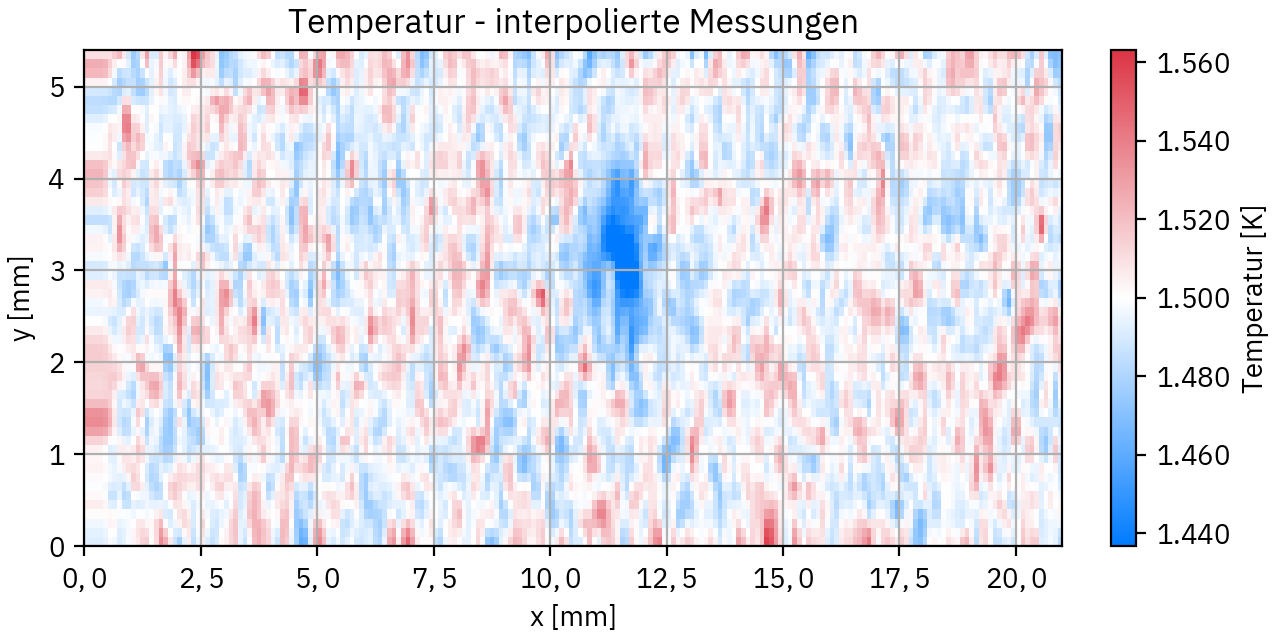
Zur Berechnung der Energiedichte muss über die Geschwindigkeit des Laserfokalpunktes noch die lokal schwankende Bestrahlungszeit berücksichtigt werden.
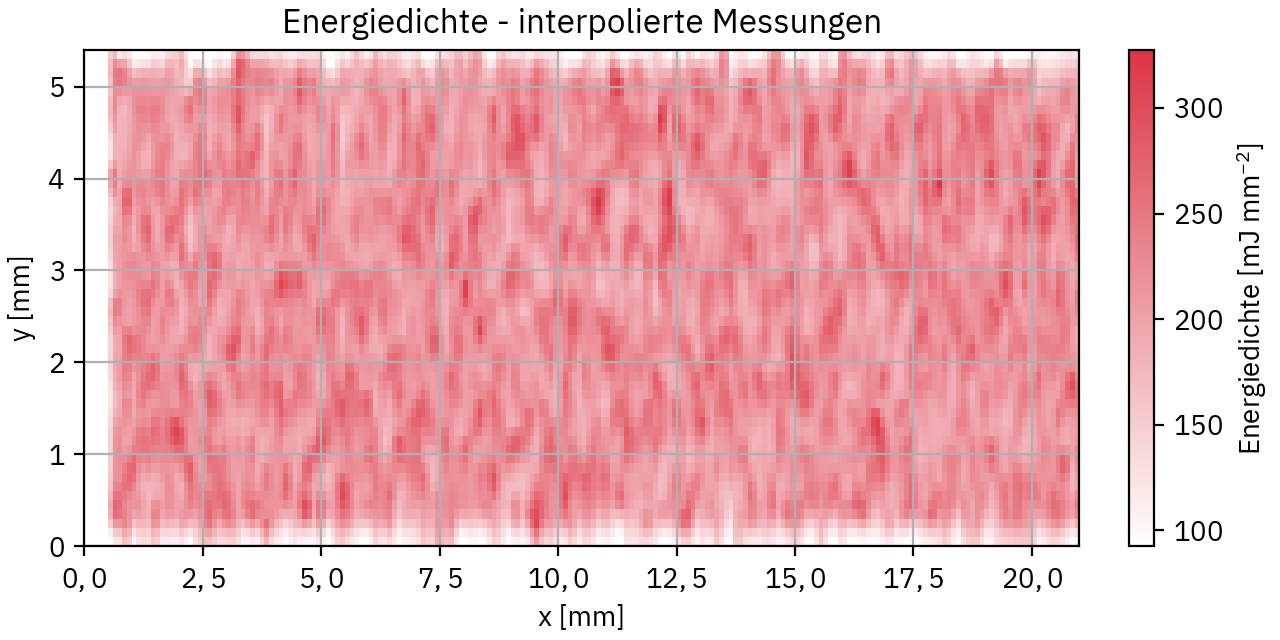
Um flexibel auf wechselnde Schwellwertprofile für komplexere Geometrien oder unterschiedliche Oberflächenstrukturen reagieren zu können, soll die Identifikation von potenziellen Fehlern aus relativer Abweichung eines Einzelprozesses zur statistischen Verteilung einer Abfolge von gleichartigen Werkstücken bestimmt werden.
Bauteilbewertung
Technische Bewertung
Mithilfe der Messreihenvergleichsmethode lassen sich zusammenhängende Bereiche identifizieren, auf denen die Messwerte signifikant außerhalb der erwarteten statistischen Schwankungen liegen. Zu diesem Zweck betrachtet man etwa die ortsaufgelöste Anomaliestärke. Sie berechnet sich aus der lokalen Mittelwertabweichung geteilt durch die lokale Standardabweichung.
Für diese abgeleitete Kennzahl kann man nun durch die Prozessphysik und die Erfahrung mit der Fertigung Größen- und Stärkenschwellwerte festlegen, welche möglichst präzise diejenigen Prozessanomalien erkennen, welche in der Qualitätsprüfung als nicht OK markiert werden sollen.
Die folgende Abbildung zeigt die Anomaliestärke sowohl für die Temperatur als auch für die Energiedichte des Beispielprozesses. In diesem Beispiel liegt auf einer zusammenhängenden Fläche von 3,59mm² eine Unterschreitung der erwarteten Temperatur um mindestens 1,2 Standardabweichungen vor. Das kann etwa durch Rückstände einer nicht entflammbaren Flüssigkeit verursacht sein.
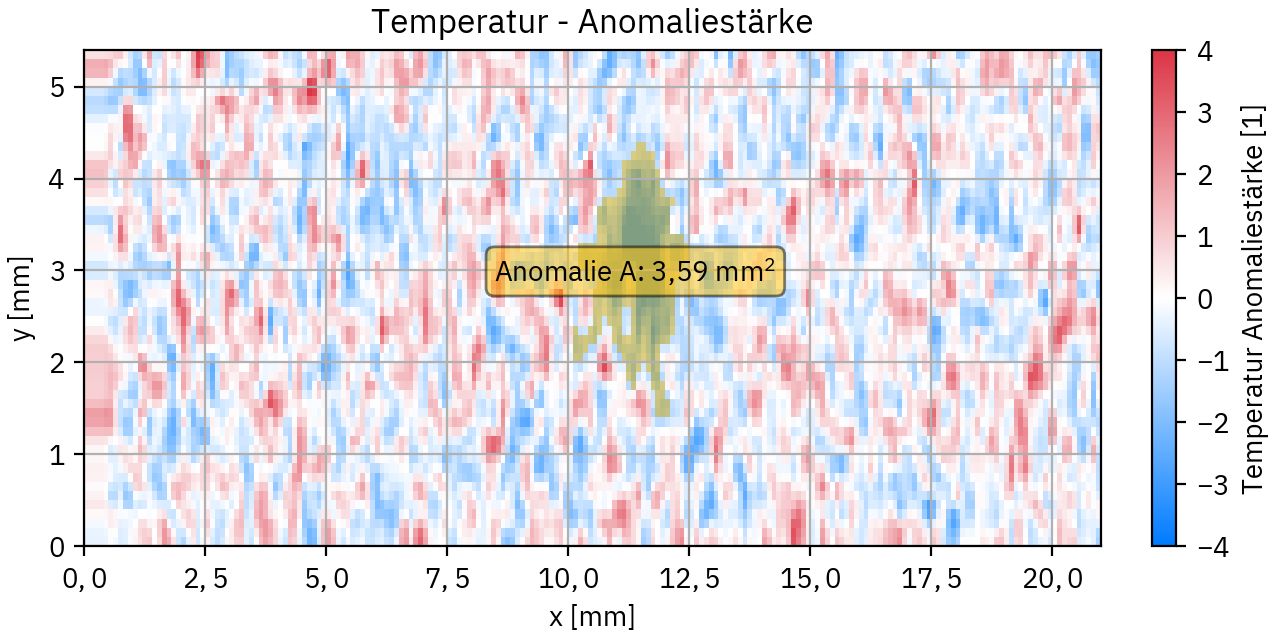
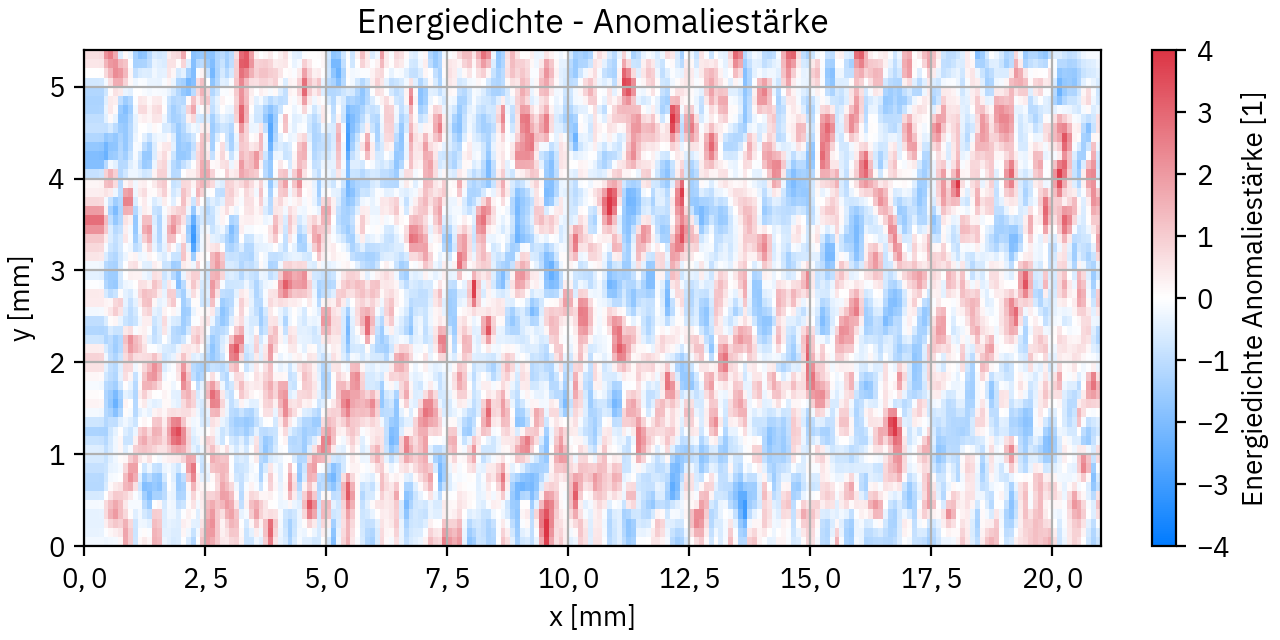
Wirtschaftliche Analyse
Um die Zuverlässigkeit der Methodik und der Schwellwerte, sowie den wirtschaftlichen Nutzen der Qualitätskennzahlen einzuschätzen, kann man die Trennschärfe der Methodik für eine Bauteilstichprobe bestimmen, deren Qualitätsmerkmale auf anderem Wege bekannt sind.
-
Defekt ausgeliefert - falsch OK
Das Bauteil ist nicht OK, aber der Fehler wird nicht bemerkt. Das Bauteil wird trotzdem ausgeliefert und verursacht Folgekosten durch Reparatur, Ersatz oder Reputationsverlust.
-
Fehlerfrei entsorgt - falsch nicht OK
Das Bauteil ist OK, wird aber fälschlicherweise anders eingeschätzt. Das Bauteil wird entsorgt und abgeschrieben, obwohl es hätte verkauft werden können.
Typischerweise sind defekt ausgelieferte Bewertungen wesentlich teurer als fehlerfrei entsorgte. Dementsprechend können die Schwellwerte genau nach betriebswirtschaftlichen Einschätzungen eingestellt werden.
Die folgende Abbildung zeigt die Verteilung für eine Stichprobe von 1.000 Bauteilen, welche mithilfe der oben beschriebenen Methode auf Temperaturanomalien untersucht wurde.
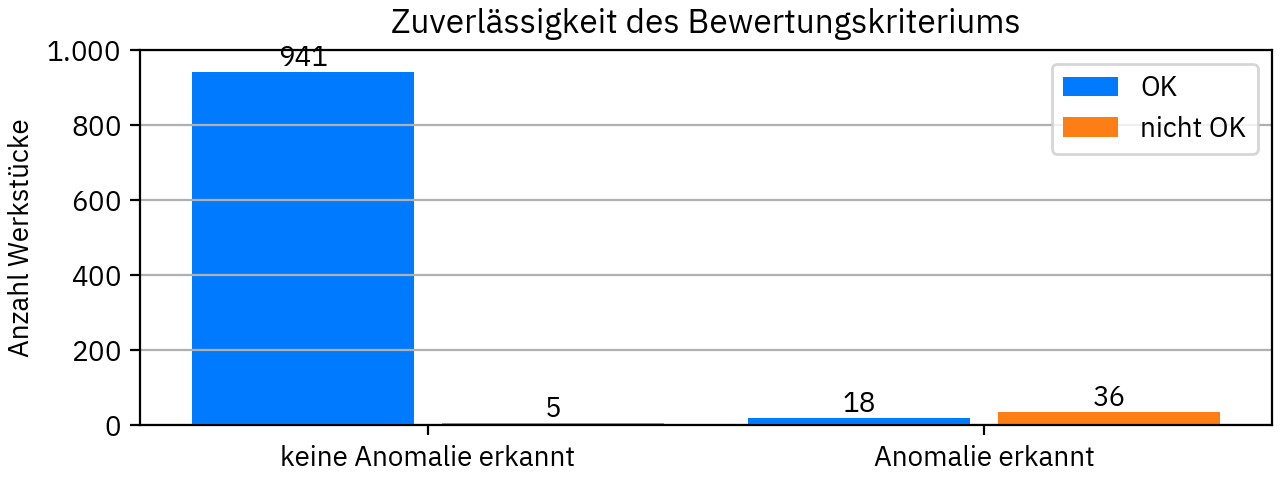
Dafür ergibt sich folgende Bewertungsgüte.
Bauteile | Bewertung | Merkmal | Anzahl | Anteil |
---|---|---|---|---|
gesamt | 1.000 | 100,0% | ||
keine Anomalie erkannt | 946 | 94,6% | ||
OK | 941 | 94,1% | ||
nicht OK | 5 | 0,5% | ||
Anomalie erkannt | 54 | 5,4% | ||
OK | 18 | 1,8% | ||
nicht OK | 36 | 3,6% |
Nimmt man nun an, dass ein defekt ausgeliefertes Bauteil Folgekosten von 10€ und ein entsorgtes Bauteil Abschreibungen von 1€ verursacht, ergibt sich damit die folgende Fehlerkostenschätzung:
QS-System | Fehlerquelle | Quote | Kosten / Fehler | Kosten / Teil |
---|---|---|---|---|
ohne oddy | 4,1% | 0,410€ | ||
defekt ausgeliefert | 4,1% | 10€ | 0,410€ | |
defekt entsorgt | 0,0% | 1€ | 0,000€ | |
fehlerfrei entsorgt | 0,0% | 1€ | 0,000€ | |
mit oddy | 5,9% | 0,104€ | ||
defekt ausgeliefert | 0,5% | 10€ | 0,050€ | |
defekt entsorgt | 3,6% | 1€ | 0,036€ | |
fehlerfrei entsorgt | 1,8% | 1€ | 0,018€ |
In diesem Szenario ergibt der Einsatz von oddy im Vergleich zu einem QS-System, welches die detaillierten Fehlerbilder nicht erkennt, eine erwartete Kostenreduktion um 74,6% durch verbesserte Qualitätskontrolle von 0,410€ auf 0,104€ pro Bauteil.
Anlagen- und Chargenüberwachung
Zusätzlich zur niedrigeren Ausfallquote in ausgelieferten Bauteilen stellt das oddy-System einen präzisen Einblick in die Prozessdaten zur Verfügung. Damit ist es möglich, laufend Prozessveränderungen zu analysieren und zu bewerten. So steht ein weiteres Werkzeug zur Verfügung, um Fehlerursachen schnell zu finden und große Qualitätsprobleme frühzeitig zu vermeiden.
Indem die Prozessdaten immer mit einem Satz Prozessdaten verglichen werden, der regelmäßig erneuert wird, lassen sich Trends in den Prozessdaten abbilden und aus deren Verteilungsbreite auch die Prozessstabilität überwachen. Dies kann frühzeitig auf Wartungsbedarf, Chargenprobleme oder Probleme in Vorprozessen hindeuten.
Die folgende Abbildung zeigt die Prozessdatenverteilung von mehreren hundert Messungen in Temperatur und Energiedichte, jeweils als Mittelwert und Standardabweichung.
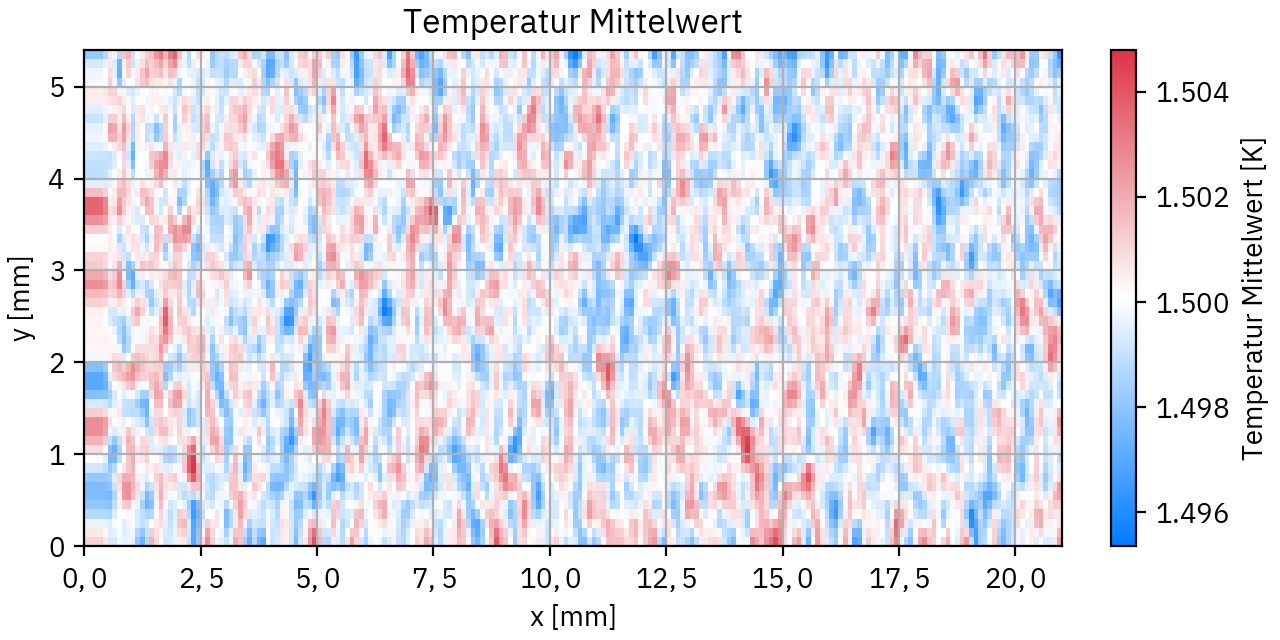
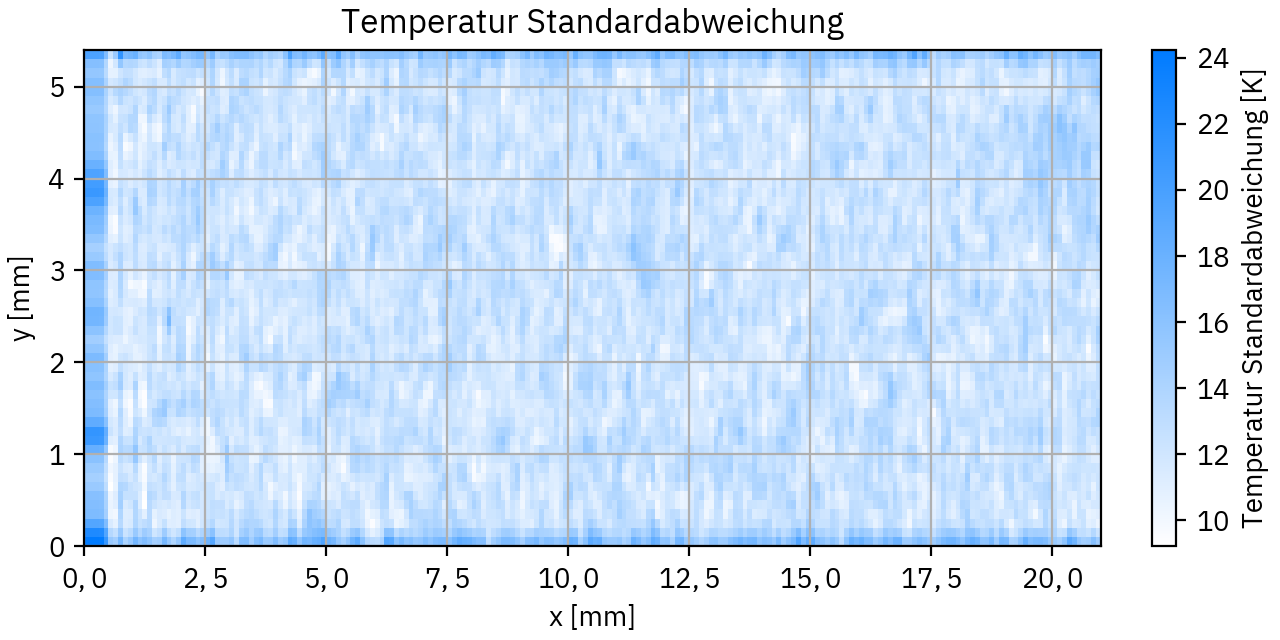
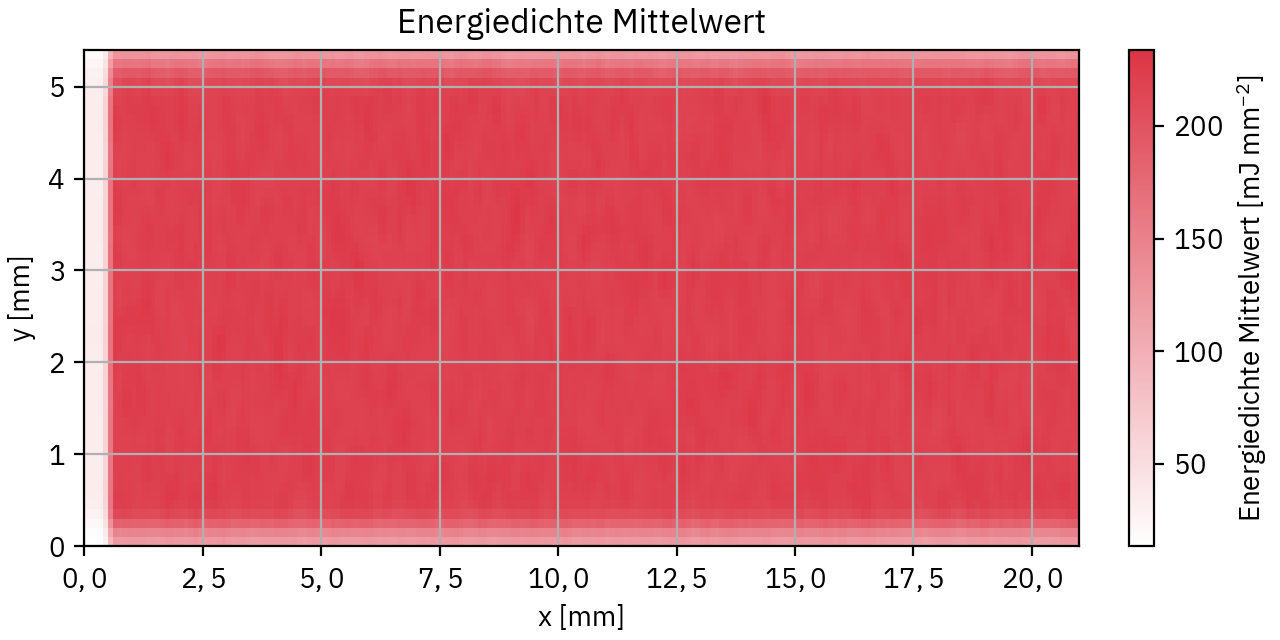
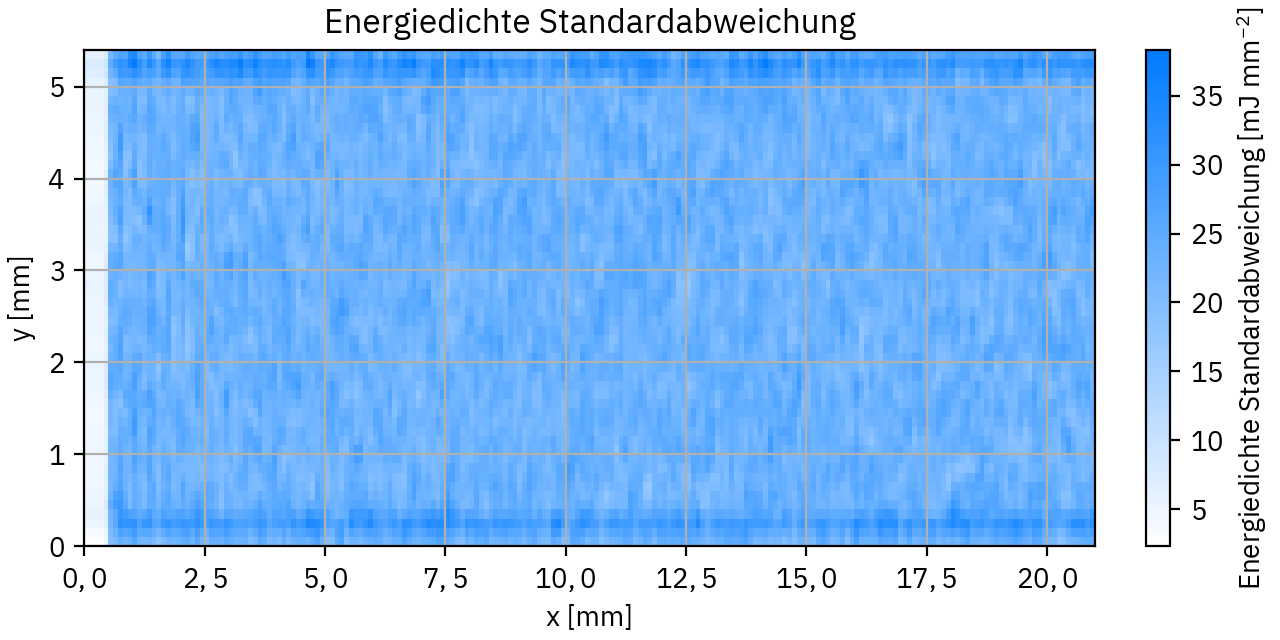
Fazit
Durch ortsaufgelöste Prozessdatenanalyse kann oddy Fehlerbilder identifizieren, welche nicht durch Analysen mit konstanten Schwellwerten gefunden werden können. Durch diesen Vorteil ist es möglich, die Fehlerfolgekosten von defekt ausgelieferten Bauteilen drastisch zu reduzieren. Zusätzlich liefern detaillierte Prozesseinblicke die Möglichkeit, frühzeitig bei Betrieb mit erhöhten Fehlerraten zu analysieren und zu intervenieren.
Die für diese Fallstudie verwendeten Prozessdaten sind zu Demonstrationszwecken streng zufällig erzeugt worden.